A bike frame is the structural foundation of a bicycle. It provides the mounting points for all other components — wheels, handlebars, seat, drivetrain, and brakes. The bike frame determines the bike's fundamental riding characteristics and purpose. Bike frames are made of steel, aluminum, carbon fiber, titanium, or combinations of these to provide a variety of stiffness, durability, and weight.
Bicycles are made of materials like steel, titanium, aluminium, carbon fiber. Some of them also use scandium-aluminum alloyed metals.
Bike frames are primarily made from metal alloys and carbon fiber. Steel is the classic choice, known for strength, comfort, affordability, and repairability. Different types of steel offer varying levels of performance and weight. Aluminum is lighter and stiffer than steel, making it popular for performance bikes, but it can offer a harsher ride.
Carbon fiber is the lightest and stiffest option, ideal for racing bikes, but it is also the most expensive and susceptible to hidden damage. Titanium is exceptionally strong, durable, and offers a comfortable ride, but its high cost makes it a premium choice.
Manufacturers sometimes combine materials to achieve specific performance goals or price points. Understanding the properties of each material and how they translate to ride feel is key when selecting a bike frame.
Frame materials are only one aspect of a bike's design. How the tubes are shaped, the geometry of the frame and the quality of manufacturing all affect the bike's ride quality and characteristics.
What Materials Are Bike Frames Made Of?
Bike frames are usually made of metallic alloys and carbon fiber. Alloys are combinations of metals to combine one metal with others to achieve the manufacturer’s desired properties. The most common materials used in bike frames are steel, aluminum, and carbon fiber. Less common materials include titanium and magnesium.
- Steel is the classic bike frame material, known for its durability and affordability compared to carbon or aluminum
- Aluminum is the second most popular choice for modern bikes due to its balance of affordability and performance.
- Carbon fiber, known for its weight savings and stiffness, is used in high-performance bikes.
- Titanium, known for its strength, and corrosion resistance is a premium material, often used in high-end, custom-built frames.
Carbon (High-Tensile) Steel is the most commonly used material in bike frames. High-tensile steels are low-carbon, or steels at the lower end of the medium-carbon range, which have additional alloying ingredients to increase their strength, wear properties or specifically tensile strength. These alloying ingredients include chromium, molybdenum, silicon, manganese, nickel, and vanadium.
Carbon or high-tensile steel is a strong, long-lasting steel, but it's not as light as chromoly.
Understanding Steel Bike Frames
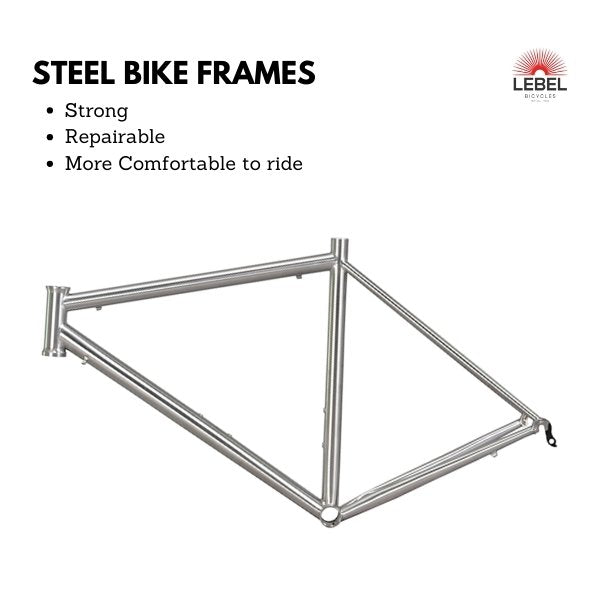
A steel bike frame uses steel alloys as its primary structural material. Steel is a combination of iron and carbon, with additional elements added to customize its properties. These elements are added to steel for strength. It's a classic material that remains popular due to its unique blend of affordability, strength, comfort, and timeless aesthetic.
Types of steel used in steel bike frames are the following.
- Chromoly (Chrome-Molybdenum): The most popular steel for bikes, offering lightness, superior strength, and a comfortable ride.
- Reynolds: A series of high-end steel alloys with specific numbers like 531, 631, and 853 (increasing performance and lightness).
- Stainless Steel: Extremely durable and rust-resistant but heavier than the other options.
- High-Tensile Steel: Used for affordable bikes; it's strong but heavier and less responsive.
Steel bike frames are strong, repairable, and provide a more comfortable ride. Steel is very resilient, able to handle impacts and daily use for years without breaking. It has inherent flex, absorbing road vibrations for a smoother feel than stiffer materials. Damaged steel frames can sometimes be bent back into shape or welded.
Compared to aluminum, steel in bike frames is heavier, typically more flexible, and more forgiving on rough roads. Steel absorbs some of the vibrations from the road, making the ride more comfortable.
Steel in bike frames is similar in comfort to titanium, which is more strong and light, but very expensive.
Which Styles of Riding Is Steel Frame Good For?
Steel is good for the following styles of riding:
Touring: Strength, comfort, and the ability to carry gear are essential.
Commuting: Durability and a comfortable ride for daily use.
Gravel Riding: Balances comfort and performance on mixed terrain.
Retro or Classic Bikes: Steel delivers that vintage cycling feel.
Steel Bike Frame Construction Types
- Lugged: Classic construction — steel tubes are joined with decorative lugs.
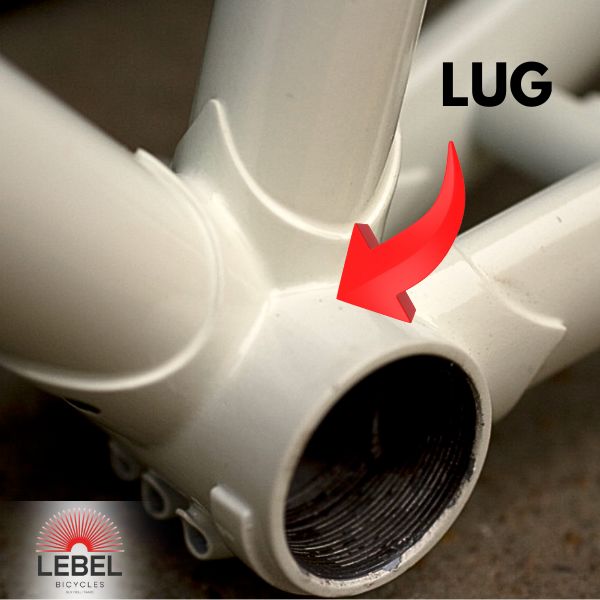
- TIG Welded: A modern technique where tubes are welded together directly.
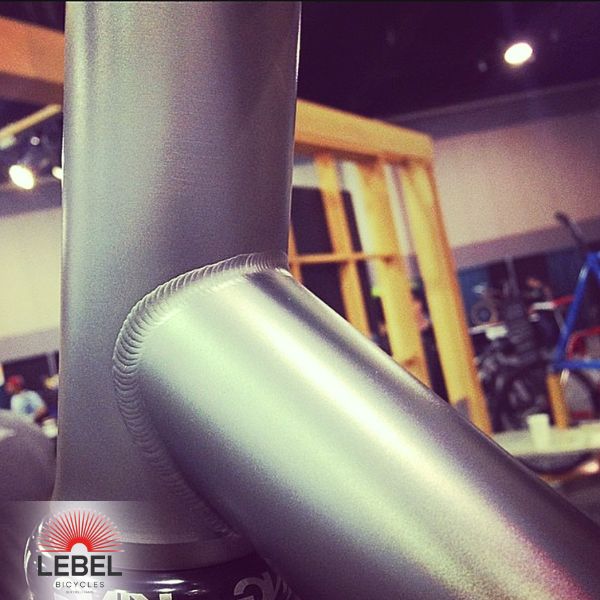
- Fillet Brazed: Creates a smooth, flowing aesthetic at the tube joints but is labor-intensive.

How Are Steel Bike Frames Made?
Steel bike frame production consists of steel alloy selection, tube preparation, tube shaping, frame assembly, and finishing.
The process of steel bike frame production is described below:
- Steel Alloy Selection:
- Chromoly: There are several grades of chromoly (like 4130, Reynolds 853), each with slightly different properties that balance between strength, weight, and ride feel.
- Stainless: Specific stainless steel alloys are chosen for corrosion resistance but bring fabrication challenges.
- Tube Preparation:
- Seamless vs. Seamed: Seamless tubes are stronger and lighter, formed by extruding and drawing solid steel billets. Seamed tubes are rolled and welded, which makes them more economical but slightly less refined.
- Butting: Many high-quality tubes have butted profiles. This means the walls are thicker at the ends (where stress is higher) and thinner in the middle, saving weight while maintaining strength. Butting can be single, double, or even triple-butted.
- Tube Shaping:
- Mitering: The ends of tubes are precision-cut with specialized machinery to create angles for joining. This can be done manually or with CNC machines for high accuracy.
- Bending/Forming: For some frame designs, tubes require bending or forming into specific shapes. This is done with specialized bending tools and heat to avoid compromising the steel's structure.
- Frame Assembly
- Lugged Construction
- Lugs (cast or machined steel sleeves) are painstakingly fitted over tube ends.
- Tubes are brazed into lugs using brass or silver filler material creating classic, strong joints.
- TIG Welding
- Tubes are aligned in jigs that ensure correct geometry.
- Skilled welders use TIG (Tungsten Inert Gas) to create precise, strong welds.
- Heat Affected Zones (HAZ) around welds are carefully managed to avoid compromising steel strength.
- Fillet Brazing
- Similar to lugged, but instead of sleeves, a fillet of brass is meticulously applied to form smooth, aesthetically pleasing joints between tubes.
- Finishing
- Alignment Check: Regardless of technique, the final frame undergoes alignment checks to ensure perfect geometry.
- Cleaning & Preparation: Chemical bathing or sanding prepares the steel for paint or protective coatings.
- Painting/Clearcoat: From simple powder coats to elaborate multi-color schemes, the final color and surface treatment are applied based on aesthetic and protective needs.
Some high-end steel frames undergo heat treatment after construction to optimize grain structure and enhance strength.
Pros Of Steel Bike Frames
- Comfort (vibration absorbtion)
- Durability
- Repairability
- Classic aesthetic
- More affordable than carbon or titanium bike frames
Cons Of Steel Bike Frames
- Heavier than most alternative
- Prone to rust (unless stainless steel is used)
Understanding Aluminium Bike Frames

Aluminum is a lightweight, readily available metal. In bike frames, aluminum is used in the form of alloys, combined with other elements to improve its properties.
Aluminum is one of the most popular bike frame materials due to its excellent blend of performance and affordability.
3 popular aluminum alloys used in bike production are:
- 6061 Aluminum: a precipitation-hardened aluminium alloy, containing magnesium and silicon as its major alloying elements. Common and affordable, offering a good balance of strength and weight.
- 7005 Aluminum: an aluminium wrought alloy used in bicycle frames. Due to its relative ease of welding, it does not require expensive heat treatment. Slightly stronger than 6061, it is often used for higher-end frames.
- Scandium-Aluminium: Features scandium for exceptional strength-to-weight ratio but comes at a higher cost.
Aluminium bike frames are significantly lighter than steel frames, making bikes easier to handle and accelerate. They are stiffer than steel, which provides better power transfer while pedaling than metal frames. Aluminium bike frames don’t rust, just like titanium. Compared to steel, aluminium is stiffer, but steel offers a smoother ride and can be more durable over time.
Which Styles of Riding Is Aluminium Frame Good For?
- Performance and Racing: Aluminum's light weight and stiffness make for snappy acceleration, excellent climbing ability, and efficient power transfer – vital for competitive road riding.
- Endurance and Sportives: While not quite as comfortable as steel or titanium, modern aluminum frames manage road vibrations well, making them suitable for long-distance rides.
- Hardtails: Aluminum hardtails are commonplace due to their stiffness and budget-friendliness, perfect for beginner and intermediate riders.
- Commuting and Urban Riding: Aluminum's robustness and affordability make it great for the daily grind, and its lighter weight helps easily navigate urban landscapes.
Aluminium Bikes Frame Construction Types
- Butted Tubes: Using of tubes in manufacturing with varying thickness – thicker at the ends where stress is higher and thinner in the middle to save weight for bike frames.
- Hydroforming: A process of using high-pressure fluid to shape aluminum tubes into complex shapes for aerodynamic or aesthetic benefits for bike frames.
How Are Aluminium Bike Frames Made?
Aluminium bike frame production consists of raw material sourcing and alloying, tube formation and preparation, frame assembly, post-welding processes, and finishing.
The process of aluminium bike frame production is described below:
- Raw Material Sourcing and Alloying:
- Aluminum Ingots: The process starts with large ingots of raw aluminum.
- Alloying Elements: Specific elements like magnesium, silicon, and sometimes scandium are added to the molten aluminum to create the desired alloy with enhanced properties.
- Tube Formation:
- Extrusion: Most aluminum tubes start as solid cylindrical billets. They're heated and forced through a die under immense pressure, creating long tubes with the desired cross-sectional shape.
- Butting: To optimize weight and strength, tubes undergo butting. This involves either mechanically thinning the tube's center (single, double, triple butting) or swaging the ends to increase wall thickness where it joins other tubes.
- Hydroforming For complex shapes, hydroforming is used. A tube is placed into a mold, and high-pressure fluid is pumped inside, forcing the aluminum to expand and take the shape of the mold. This allows for aerodynamic profiles or intricate frame designs.
- Tube Preparation
- Cutting and Mittering: Tubes are cut to precise lengths and angles using specialized saws or CNC machines. The ends are often mitered (angled cuts) to ensure a perfect fit when joining frame sections.
- Machining: Areas, where components will attach (head tube, bottom bracket, dropouts), may be machined to ensure accurate dimensions and smooth surfaces.
- Frame Assembly
- Jigging: Tubes are carefully placed in a precise jig to ensure the correct alignment of the frame's sections.
- Tack Welding: Small welds are made to temporarily hold the tubes in position.
- Welding: Most aluminum frames use TIG (Tungsten Inert Gas) welding. With meticulous technique, a welder joins the tubes permanently, creating strong bonds.
- Post-Welding Processes
- Heat Treatment: Many aluminum alloys undergo heat treatment (e.g., T6 temper) to further increase their strength and relieve stress from the welding process.
- Alignment Check: The frame is checked again on a jig to ensure it meets precise tolerances.
- Finishing
- Sanding and Smoothing: Welds are sanded and smoothed for a clean appearance and to remove any stress risers.
- Painting or Anodizing: The frame receives either a durable paint coating in various colors or an anodized finish for a corrosion-resistant and often colorful surface.
- Decals: Manufacturer branding and model decals are applied.
Pros Of Aluminium Bike Frames
- Affordability
- Great strength-to-weight ratio
- Corrosion resistance
- Availability
Cons Of Aluminium Bike Frames
- Harsher ride compared to steel or titanium frames
- Can be prone to fatigue over very long periods
- Very difficult to repair
Understanding Carbon Fiber Bike Frames
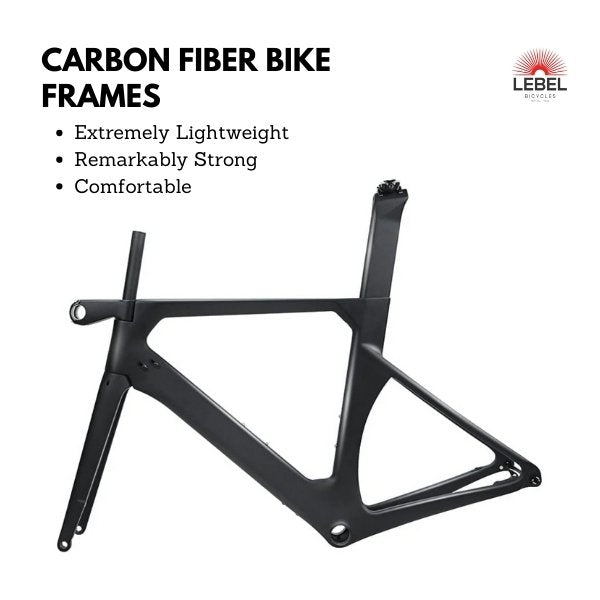
Carbon fiber bike frames are made of carbon fiber composites, where thin strands of carbon are woven into fabric and bonded with a strong resin. This results in an incredibly lightweight yet remarkably strong and stiff material.
While classifications of carbon fiber frames are not always strictly defined, carbon fiber frames can vary based on:
- Carbon Fiber Modulus: Higher modulus carbon is stiffer but more brittle. Frames mix high and lower modulus fibers for optimal performance and cost.
- Weaves: Carbon fiber can be woven in different patterns (unidirectional, woven) providing different characteristics.
Carbon fiber bike frames are significantly lighter than aluminum, but aluminum frames can be more affordable. Carbon fiber frames offer superior strength-to-weight ratio and vibration damping compared to steel frames. Similar to carbon in some ways, the titanium bike frames are heavier than carbon fiber but offer unique flex and durability.
Carbon fiber construction types include:
- Monocoque: Frame molded mostly as a single piece for seamless strength.
- Tube-to-Tube: Individual carbon tubes bonded together, allowing greater customization.
Which Styles of Riding Is Carbon Fiber Frame Good For?
Carbon fiber frames are good for performance riding:
- Road Racing: for lightness and stiffness.
- Endurance Road: for comfort with efficiency.
- Mountain Biking: for lightness (trail and XC bikes).
How Are Carbon Fiber Bike Frames Made?
Carbon fiber bike frame production consists of design and engineering, prepreg preparation, molding and layup, curing, and finishing.
- Design and Engineering
- Virtual Modeling: Engineers use CAD software to design frame shapes, tube profiles, and carbon fiber layup schedules. This optimizes strength, weight, and stiffness in specific zones.
- Finite Element Analysis (FEA): Simulations test the frame's response to various stresses and loads, ensuring it meets safety and performance standards.
- Prepreg Preparation
- Prepreg Sheets: Carbon fiber fabrics are pre-impregnated with epoxy resin. These sheets are meticulously cut to the patterns designed for each section of the frame.
- Precision is Key: The orientation of fibers (unidirectional, woven, etc.) within each prepreg layer is critical to achieving the desired frame characteristics.
- Molding and Layup
- Monocoque Molds: For monocoque frames, large complex molds determine the entire frame shape. Internal bladders can be used for pressure during curing.
- Tube-to-Tube Molds: Individual tube sections have their own molds. Prepreg is laid up inside or around the molds for each part (head tube, top tube, etc.).
- Hand Layup: Skilled technicians carefully place each prepreg layer within the mold, ensuring correct alignment and avoiding wrinkles or gaps.
- Curing
- Heat and Pressure: Molds are placed in ovens or autoclaves (for precise high pressure). This activates the resin, bonding the carbon fiber layers and curing the composite.
- Controlled Environment: Temperature and pressure are precisely controlled to ensure optimal curing and material strength.
- Finishing
- Demolding: The cured frame is carefully removed from the mold.
- Sanding and Inspection: Excess material is sanded away, and the frame undergoes rigorous quality control checks.
- Component Mounts: Areas for attaching components (derailleurs, bottle cages, brakes) are drilled or integrated during the original layup.
- Paint and Graphics: The frame receives protective paint and its final aesthetic design.
Pros Of Carbon Fiber Bike Frames
- Incredibly light yet strong and stiff.
- Carbon fiber absorbs vibrations better than some metals.
Cons Of Carbon Fiber Bike Frames
- High Cost (the most expensive frame material)
- Potential for Hidden Damage - impacts can cause unseen internal damage.
- Less Forgiving - harsher than some steel or titanium frames.
Understanding Titanium Bike Frames
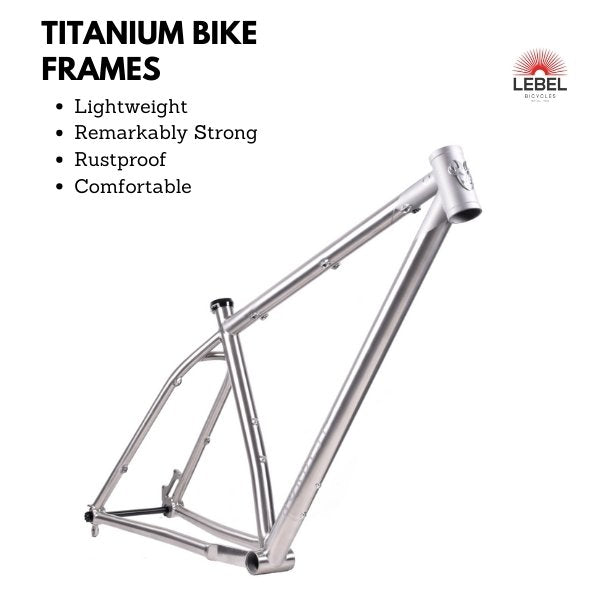
Titanium bike frames are made of titanium, a metal known for its exceptional strength-to-weight ratio, corrosion resistance, and a comfortable, lively ride feel.
While not as diverse as steel or aluminum, titanium frames do have some distinctions:
- Grade: Most commonly Grade 9 (3Al/2.5V Titanium), offering a balance of properties. Lower grades may exist for affordability, while aerospace-grade titanium offers the ultimate performance at a higher cost.
- Butting: Tubes can be butted (varying wall thickness) for optimum weight and stiffness in different areas of the frame.
Titanium bike frames don’t rust or corrode, making them a lifetime investment. They have superior fatigue resistance compared to other metals. Titanium bike frames are lighter than steel with comparable strength, but not as light as carbon fiber. Titanium offers a degree of natural vibration dampening, smoothing out some road imperfections.
Titanium frames are among the most expensive on the market due to the material cost and complex fabrication process. Expect a high starting point with premium bikes surpassing the cost of many carbon fiber models.
Pros Of Titanium Bike Frames
- Unmatched durability
- Superior ride quality
- Lightness and strength
- Lifetime investment
Cons Of Titanium Bike Frames
- High cost
- Limited repairability (compared to steel)
Understanding Mixed-Material Bike Frames
Mixed-material bike frames combine two or more different materials, usually steel, aluminum, titanium, and carbon fiber. This approach allows manufacturers to harness the strengths of each material, placing them strategically to achieve specific ride characteristics and performance goals.
Here are the examples of mixed-material bike frames:
- Carbon/Aluminum: One of the most common combinations, offering the stiffness and lightness of carbon fiber with the affordability and impact resistance of aluminum.
- Carbon/Titanium: Pairs the vibration-damping and elegant aesthetic of titanium with the stiffness and weight savings of carbon fiber.
- Steel/Titanium or Steel/Carbon: Less common, but these combinations leverage the classic feel and compliance of steel with the enhanced stiffness or weight benefits of titanium or carbon fiber.
Mixed-material frames often provide a middle ground between the lightness of full carbon and the higher weight of steel or aluminum. The carbon fiber component typically drives overall stiffness, with strategic use of other materials for tailored performance. Aluminum and titanium inserts can boost longevity in high-stress areas compared to full carbon frames. Mixed-material frames can expertly balance stiffness for responsiveness with compliance and vibration damping for comfort.
Mixed-material bike frames generally fall between the cost of full carbon and traditional steel or aluminum.
Mixed-Material Bike Frame Construction Types
- Tube-to-tube bonding: Different material tubes are joined using adhesives and sometimes external wraps.
- Lugged or welded joints: Metal lugs or welds connect tubes (especially steel and titanium combinations).
- Internal inserts: Aluminum or titanium inserts reinforce high-stress areas of primarily carbon fiber frames.
Pros Of Mixed-Material Bike Frames
- Custom ride qualities by combining material strengths.
- A good compromise between price and characteristics.
- Enhanced Durability in some key areas compared to all-carbon setups.
Cons Of Mixed-Material Bike Frames
- Can be slightly heavier than full carbon equivalents.
- Manufacturing complexity
- Potential for galvanic corrosion: Requires careful design to prevent dissimilar metals from reacting.
What Is Bike Geometry?
Bike geometry is the precise arrangement of a bicycle's frame tubes and components. Bike geometry determines how a bike will look, feel, and handle.
Measurements in bike geometry include:
- Wheelbase: The distance between the centers of the front and rear wheels. A longer wheelbase offers greater stability, especially at speed, while a shorter wheelbase provides more agility and maneuverability.
- Reach & Stack:
- Reach: Horizontal distance from the bottom bracket to the top center of the head tube. Influences how stretched out your torso is on the bike.
- Stack: Vertical distance between the bottom bracket and the top center of the head tube. Determines handlebar height.
- Head Tube Angle: Angle of the head tube (where the fork connects) relative to the ground. A steeper angle leads to quicker, more responsive steering, while a slacker angle promotes stability.
- Seat Tube Angle: Angle of the seat tube relative to the ground. Affects your position over the pedals and power transfer efficiency.
- Trail: The distance between where a line through the steering axis intersects the ground and the point where the tire contacts the ground. Trail influences how stable the bike feels when steering.
- Fork Offset/Rake: The distance the front axle sits in front of the line going through the fork. Impacts trail and steering feel.
- Chainstay Length: Distance between the rear axle and the bottom bracket. Shorter chainstays create snappier handling.
- Bottom Bracket Drop: Distance of the bottom bracket below an imaginary line between the axles. Affects pedal clearance when cornering.
How Bike Geometry Affects The Ride?
Bike geometry dictates a bicycle's handling characteristics, riding position, and overall feel.
For example, bikes with longer wheelbases, and slacker head tube angles offer increased stability at speed and on descents. In contrast, shorter wheelbases and steeper head tube angles create a more agile bike for quick turns.
Another example is that higher stack and shorter reach measurements result in a more upright riding posture, promoting comfort for longer rides and casual cycling.
A bike with a steep head tube angle, shorter chainstays, and less trail will respond very quickly to steering input, leading to a nimble and lively ride.
A steeper seat tube angle allows for a more aggressive, pedal-centric position, maximizing power transfer for racing and climbing.
Mountain bikes designed for rugged terrain often feature slack head tube angles, longer wheelbases, and ample trail for confident descents and stability in rough conditions.
Bike geometry is not about 'good' or 'bad'. It's about matching the bike's characteristics to your desired riding style, body proportions, and the terrain you'll ride on.